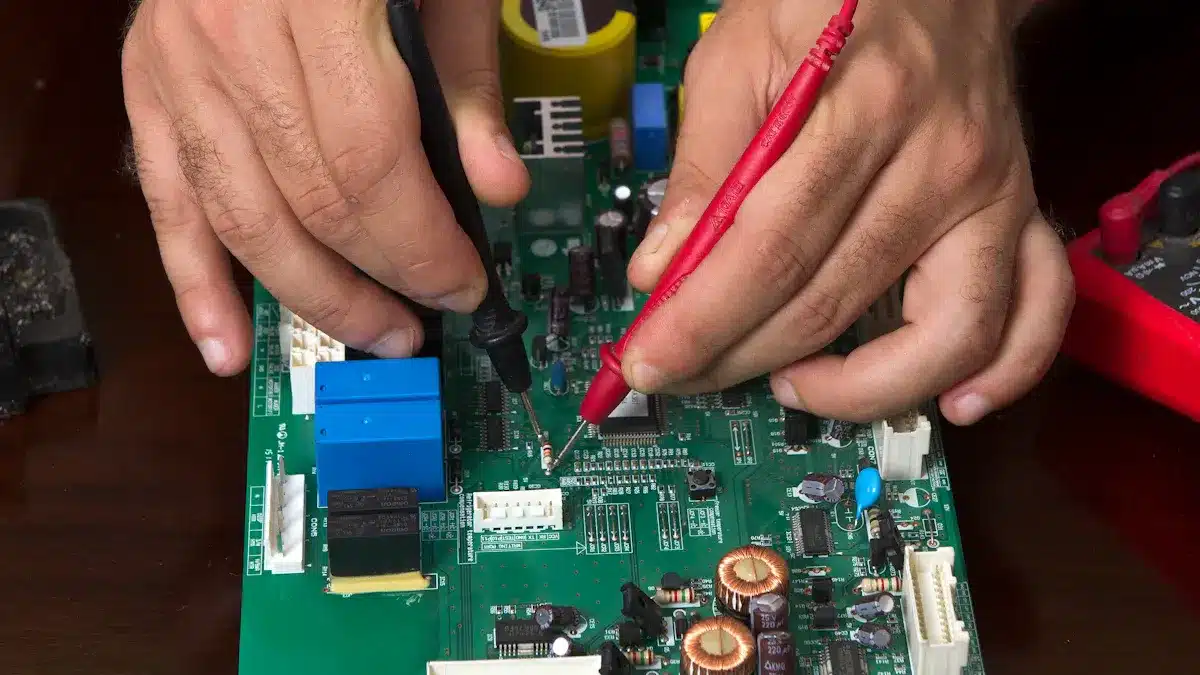
AOI, ICT, and AXI are all crucial components in PCB assembly quality control in 2025. AOI quickly and accurately inspects the surface of printed circuit boards, while AXI detects hidden issues beneath parts that AOI cannot see. ICT identifies electrical problems that both AOI and AXI might overlook. The PCB assembly market is rapidly expanding worldwide due to increasing demands in automotive, aerospace, and robust electronics sectors. Automated optical inspection and AI-driven machines have become widespread, especially in the Asia-Pacific region, where smart factories utilize advanced inspection techniques to produce higher-quality products.
Integrating these inspection methods significantly enhances PCB assembly quality control, resulting in more reliable and defect-free boards.
Key Takeaways
AOI, ICT, and AXI each find different PCB problems. Using all three together gives the best quality and fewer mistakes. AOI finds surface issues fast, like missing parts or bad solder. This makes it great for quick production lines. AXI uses X-rays to find hidden problems inside boards. This is very important for complex or layered PCBs. ICT checks electrical connections to make sure the board works right. It finds faults that visual tools cannot see. AI-based inspection makes checks faster and more correct. It helps factories find more problems early and make fewer mistakes.
Importance in PCB Assembly Quality Control
Quality Assurance Goals
Manufacturers want to make sure their products are high quality. They set goals to make sure every pcb assembly is reliable. These boards must meet what customers and the industry expect. Many companies use the ISO9001 quality system to check each step. They look at every board and do electrical tests to find problems early.
Finding defects early helps lower mistakes and saves money.
AOI systems use cameras to spot missing or wrong parts and soldering problems.
X-ray inspection can find hidden problems inside complicated or layered pcbs.
Functional testing checks if the pcb works right in real situations.
In-circuit testing looks at electrical parts and finds shorts or open spots before the last test.
Companies want to keep getting better and make customers happy. They use inspection data to fix their process and make better products.
Inspection Challenges
PCB assembly has many inspection problems as designs get harder. More surface mount technology and double-sided boards mean more hidden problems. Makers need to check both the outside and inside of printed circuit boards.
Challenge Area | Description | Inspection-Related Solutions |
---|---|---|
Complex PCB Designs | Boards have tight spaces and hidden solder joints | |
BGA & Fine-Pitch Components | Parts are close together and have hidden links | X-ray inspection, better placement, fiducial markers |
Solder Paste Printing | This SMT step causes most defects | Automated SPI, better stencil design |
Component Placement Accuracy | Machines can drift or feeders can move wrong | Regular calibration, better vision systems |
Reflow Soldering | Needs exact temperature control | Thermal profiling tools, nitrogen ovens |
Mixed Technology Assembly | Using both SMT and through-hole parts is harder | Selective soldering, special fixtures |
Automation & Industry 4.0 | Keeping quality high in complex builds | AI-driven inspection, real-time checks, digital twins |
Artificial intelligence and IoT help watch the process as it happens. These tools find and fix problems right away. This makes inspection faster and more correct. So, makers can lower the chance of product failures and make their pcbs better.
Main Equipment Types
Modern PCB assembly lines use many inspection tools. Each tool looks for certain problems and helps at different steps. The table below shows the main tools and what they do:
Equipment Type | Primary Function |
---|---|
Automated Optical Inspection (AOI) | Uses cameras and software to find problems like parts in the wrong place, missing pieces, and bad soldering by checking pictures against good examples. |
Checks each part and connection for shorts, opens, and electrical values to make sure everything works right. | |
X-ray Testing System (AXI) | Uses X-rays to look inside the PCB for hidden problems like bad solder or parts not lined up that you can’t see from outside. |
Visual Inspection | People look at the board with magnifiers to find surface problems. |
AI-Based Inspection | Uses machine learning and computer vision to spot problems faster and more accurately. |
NDT Methods | Uses thermal imaging and ultrasonic testing to find inside problems without hurting the PCB. |
AOI Overview
AOI uses special cameras and lights to scan the board’s surface. It checks each board against a good picture to find missing parts, bad solder, or wrong direction. AOI often uses AI to help find more problems and make fewer mistakes. Lights from different angles and barcodes help track boards and make checks better. AOI is best for SMT assembly, checking solder, and finding problems early.
ICT Overview
ICT uses test probes to check electrical values at certain spots. It looks for shorts, opens, wrong values, and missing parts. ICT finds bad solder, parts in the wrong way, and other faults. This tool gives fast, automatic results and shows where the problem is. ICT is important for checking if circuits work and if parts are in the right place.
AXI Overview
AXI, or automated X-ray inspection, uses X-rays to see inside the board. It finds hidden problems like empty spots in solder, solder bridges, and parts not lined up under BGAs or CSPs. This tool does not hurt the board and works well for small, crowded boards. AXI finds problems that AOI and ICT can’t see, so it is important for industries that need very good boards.
Visual Inspection
Visual inspection means people look for problems on the board’s surface. They use magnifiers or microscopes to check for bad solder, missing parts, and things you can see. This way is simple and cheap but people can make mistakes and can’t see hidden problems. Visual inspection works best with other automatic tools.
AI-Based Inspection
AI-based inspection uses machine learning to look at board pictures and find small problems. These systems work right away and connect to factory computers for easy watching. AI helps find misplaced parts, solder bridges, and missing pieces. Makers use AI checks at many steps to fix mistakes and make better boards.
NDT Methods
Non-destructive testing, or NDT, uses thermal imaging and ultrasonic testing. These ways find inside problems like cracks or layers coming apart without breaking the board. NDT helps AOI, ICT, and AXI by finding more problems in tricky boards.
AOI, ICT, and AXI work together to check everything. AOI finds surface problems, ICT checks if circuits work, and AXI finds hidden issues. Using all these checks makes sure PCB assemblies are good and less likely to fail.
How AOI, ICT, and AXI Work
AOI Principles
AOI uses special cameras to look at the board’s surface. The cameras take clear pictures using different lights, like LED or infrared. The system checks these pictures against saved good examples. It uses computer programs to find things that do not match. If something is wrong, it marks the spot. Problems can be missing parts, bad solder, or scratches. People can look at the marked pictures and stop the line if needed.
Some AOI systems use 3D pictures to check how high or thick the solder is. This helps find problems like uneven solder or parts that are not flat. AOI is good for checking the top of the board and finds many problems early. But AOI cannot see under parts or inside the board.
AOI helps check boards faster and better. It is important for finding surface problems in PCB assembly.
ICT Principles
ICT checks the board by testing its electrical parts. It uses a fixture with many small pins that touch the board. Each pin sends signals and measures things like resistance, voltage, and capacitance. The test program tells the system what numbers are okay.
The system sends signals to the board.
It checks how each part reacts.
It looks at the results and compares them to what is expected.
The system finds shorts, opens, wrong values, or missing parts.
It makes reports so workers can fix the problems.
ICT is very good at finding electrical problems and checking if parts are in the right place. It works best for making lots of boards. But setting up ICT can cost a lot and is not easy for small jobs.
AXI Principles
AXI uses X-rays to look inside the board. The X-rays go through the board and make pictures. Different things inside the board block the X-rays in different ways. This makes the pictures show what is inside, like solder and wires.
AXI software checks the pictures and compares them to perfect models.
It finds hidden problems like empty spots in solder, bridges, parts not lined up, and cracks.
3D X-ray CT makes 3D pictures for better checking.
AI helps the system tell real problems from mistakes.
AXI does not hurt the board and is good for tricky boards with BGAs or many layers. It is used in places like cars and planes, where hidden problems can be very bad.
Strengths and Weaknesses
AOI Pros and Cons
AOI is very good at finding problems on the top of PCBs. It uses sharp cameras and bright lights to spot things like missing parts or solder bridges. AOI checks boards fast and does not touch them. This makes it great for checking boards as they move down the line. AOI gives the same results every time and makes reports to help fix problems. It finds problems early, so companies do not have to redo work or waste money.
Pros:
Finds missing parts and lifted leads well
Always gives the same results, people do not get tired
Makes reports so you can track problems
Works well for tricky boards and small parts
Cons:
Cannot see under BGAs or inside the board
Sometimes says there is a problem when there is not, or misses real problems, so it needs updates
Costs a lot to buy, especially the best ones
Only checks what you can see, not how strong the solder is
ICT Pros and Cons
ICT looks for electrical problems. It uses pins to test for shorts, open spots, or wrong values. ICT is good for making lots of boards and gives the same answer every time. It can check each part, even BGAs and FPGAs, and stops bad boards from leaving the factory.
Pros of ICT | Cons of ICT |
---|---|
Always gives the same results | |
Finds problems fast and well | Takes longer to set up and get ready |
Does not break often and does not stop working much | Needs special spots on the board for testing |
Checks each part and measures values | Cannot check connectors or parts that are not electrical |
Makes fewer mistakes than people | Only finds electrical problems, not all solder problems |
ICT cannot find some solder problems, like empty spots or too much solder. It also does not check if parts work together in real life.
AXI Pros and Cons
AXI uses X-rays to look inside boards. It is great for finding hidden problems. AXI can see solder problems under BGAs, QFNs, and other parts that AOI cannot check. It is very good at finding problems inside, like empty solder spots or pins that are not lined up.
Pros:
Finds hidden problems and checks solder inside
Works well for busy boards with lots of parts
Does not hurt the board and is good for important jobs
Cons:
Slower than AOI and costs more to use
Does not check if the board works right
Needs trained people and must be checked often
AXI helps AOI and ICT by finding problems they miss.
Visual & AI-Based Pros and Cons
Visual inspection means people look for problems. They can find easy-to-see problems but miss small or hidden ones. People get tired, so the results are not always the same and there are more mistakes.
AI-based inspection uses computers to find problems. These systems do better than people. They find more real problems and make fewer mistakes. AI works faster and does not get tired.
Method | True Positive Rate | False Positive Rate | Speed (relative) |
---|---|---|---|
AI-Based | ~81% (F1-score) | 2.7% | 1.5x faster |
Commercial Tool | 83.3% | 8.0% | Baseline |
AI-based inspection helps find more problems, makes fewer mistakes, and works faster. This makes it a good choice for new PCB assembly lines.
Comparison in PCB Assembly Quality Control
Capabilities Table
Picking the right inspection tool for pcb assembly quality control means knowing what each one does best and where it falls short. The table below shows how AOI, AXI, ICT, and other inspection ways compare in important areas:
Aspect | AOI (Automated Optical Inspection) | AXI (Automated X-ray Inspection) | ICT (In-Circuit Test) | Visual Inspection | AI-Based Inspection |
---|---|---|---|---|---|
Inspection Method | Looks at the board’s surface with cameras | Uses X-rays to see inside the board | Tests electrical parts and paths | People look at the board | Uses computers and machine learning |
Defect Detection | Finds missing or wrong parts, solder bridges, and polarity mistakes | Finds hidden problems like solder voids and cracks | Finds shorts, opens, and wrong values | Finds things you can see | Finds surface and pattern problems |
Inspection Depth | Only checks what you can see on top | Can see inside and through layers | Checks electrical paths and parts | Only looks at the surface | Checks surface and some patterns |
Speed and Throughput | Checks boards fast, works as boards move down the line | Slower, often checks just some boards | Fast for big groups, but slow to set up | Slow, depends on the person | Fast and works in real time |
Cost | Costs less to buy and run | Costs more and needs safety for X-rays | Costs a lot to set up, runs at a medium price | Cheap but needs lots of workers | Costs medium to high, depends on system |
Application Areas | Used for SMT lines and big jobs | Used for tricky boards in cars, planes, and medical stuff | Checks if boards work after building | Good for small jobs and testing | Used in smart factories |
Limitations | Can’t see inside, needs good lighting | Takes longer, needs skilled people and X-ray safety | Can’t see visual problems, needs test spots | People make mistakes, not good for big jobs | Needs lots of training data, may miss rare problems |
AOI and AXI both use ways that do not hurt the board. AOI is great for finding surface problems fast. AXI finds hidden problems inside printed circuit boards. ICT checks if the board works right, and AI-based inspection makes finding problems faster and more correct.
Application Scenarios
Each inspection tool works best at a certain step in pcb assembly. Makers often use more than one tool to check for all kinds of problems.
AOI
AOI is best for SMT lines and fast jobs. It checks boards after solder paste, after putting on parts, and after soldering. AOI finds missing parts, solder bridges, and polarity mistakes on the surface. It gives quick feedback so workers can fix things fast.AXI
AXI is needed for boards with hidden solder joints, like BGAs or crowded boards. It checks inside layers and finds voids, cracks, and parts not lined up. AXI is used in cars, planes, and medical devices where boards must work well.ICT
ICT checks if the board works after it is built. It looks for shorts, opens, and wrong values in parts. ICT is important to make sure the pcb works as it should. It does not show if solder joints are good, but it tells if the board passes electrical tests.Visual Inspection
Visual inspection is good for small jobs, test boards, or last checks. People use magnifiers to look for problems they can see. This way is not as good for big jobs because people get tired and make mistakes.AI-Based Inspection
AI-based inspection helps smart factories and new Industry 4.0 ideas. It uses machine learning to find surface and pattern problems faster than people. AI systems learn new problems and give data to help make better boards.
Key points for picking inspection tools:
AOI checks surface problems fast and well for SMT and mixed lines.
AXI finds hidden problems in tricky, layered boards.
ICT makes sure the board works and passes tests.
Visual inspection is cheap for small jobs.
AI-based inspection makes checking faster and more correct in new factories.
Makers get the best quality by using AOI, AXI, and ICT together during pcb assembly. This way, they find all main problems and keep quality high.
Selection Guide
Key Factors
Picking the right inspection equipment for pcb assembly is important. Companies need to think about how they make boards and the final product. This helps them get good quality and boards that work well. Here are some main things to think about:
New inspection tools like aoi and X-ray inspection help find problems early.
Following rules like ISO 9001, IPC-A-610, and AS9100 shows a company cares about quality.
Doing tests in the factory, like functional test, in-circuit test, and stress testing, helps catch problems before shipping.
Suppliers who know a lot about the industry can help make better boards.
Using new machines, like automated pick-and-place, solder paste printers, and reflow ovens, makes work more exact and faster.
Companies should check if makers have ISO and UL certificates and use good tests like aoi, X-ray, and electrical testing.
Being able to build tricky printed circuit boards and make lots of them keeps quality the same.
Testing a few boards before making many helps make sure the process works.
Using both people and machines to check boards at different steps stops big mistakes and keeps the company’s name good.
Tip: Companies that buy good inspection tools and follow strict rules have fewer problems and make customers happier.
Decision Matrix
A decision matrix helps companies pick the best inspection tool for their needs. The table below shows what each tool is good at and matches it with what the process needs:
Process Requirement | AOI | AXI | ICT | Visual Inspection | AI-Based Inspection |
---|---|---|---|---|---|
Surface defect detection | ✅ Excellent | ⚪ Good | ⚪ Limited | ⚪ Limited | ✅ Excellent |
Hidden defect detection | ⚪ Limited | ✅ Excellent | ⚪ Limited | ❌ Not possible | ⚪ Limited |
Electrical test | ❌ Not possible | ❌ Not possible | ✅ Excellent | ❌ Not possible | ❌ Not possible |
Speed for mass production | ✅ High | ⚪ Medium | ✅ High | ❌ Low | ✅ High |
Flexibility for prototypes | ⚪ Medium | ⚪ Medium | ❌ Low | ✅ High | ✅ High |
Cost efficiency | ✅ Good | ❌ High cost | ⚪ Medium | ✅ Excellent | ⚪ Medium |
Process improvement data | ✅ Yes | ✅ Yes | ✅ Yes | ❌ No | ✅ Yes |
Note: Companies should pick equipment that matches what they need most to get the best results in pcb assembly quality control.
AOI, AXI, and ICT each find different problems on PCBs. The table below shows what each one is good at:
Defect Type | AOI | AXI | ICT |
---|---|---|---|
Open Circuits | ✅ | ✅ | ✅ |
Solder Voids | ❌ | ✅ | ❌ |
Incorrect Component Value | ❌ | ❌ | ✅ |
Makers should pick the right tool for their job.
AOI works best for fast lines with lots of boards.
AXI is great for tricky boards with hidden parts.
ICT is used to find electrical problems.
FAQ
What is the main difference between AOI and AXI?
AOI uses cameras to check the top of PCBs. AXI uses X-rays to see inside the board. AOI finds problems you can see on the surface. AXI finds hidden problems under parts. Both help make boards better.
How often should manufacturers calibrate inspection equipment?
Manufacturers need to check their inspection tools often. Most experts say to do this every month. Checking tools often keeps results correct and helps catch more problems.
Can AI-based inspection replace human inspectors?
AI-based inspection works faster and finds more problems. It can spot things people might not see. But people are still needed for hard or rare problems.
Which inspection method works best for prototypes?
Visual checks and AI-based systems are good for prototypes. They are easy to set up and can change fast. AOI and ICT take more time and work for small groups of boards.
See Also
Improving Quality Assurance Throughout The PCBA Workflow
Discovering Effective PCBA Testing Methods For Modern Electronics
Guaranteeing High Quality And Efficiency In PCBA Manufacturing
Top Ten Professional Tips For Cost-Effective PCBA Assembly
Choosing PCBA Production Providers With Cutting-Edge Features